High-Strength PLA Filament for Functional Parts: Is It a Game Changer?

Introduction: PLA’s Reputation and the High-Strength Paradox
High-Strength PLA Filament? Strong? Yeah, right.
For years, PLA has been the beginner’s filament—easy to print, decent-looking, but far from what you’d call “high strength.” If you need functional parts, you’re told to reach for ABS, Nylon, or Polycarbonate. PLA, with its brittle nature and low heat resistance, was best left to decorative models and casual prints.
Yet here we are, talking about high-strength PLA as if it could suddenly go toe-to-toe with engineering-grade materials. Is it just marketing hype, or has PLA actually evolved into something more durable?
In this blog post, we’ll challenge its reputation and explore whether reinforced PLA blends can hold their own in functional applications. Will it ever replace ABS or Nylon for load-bearing parts? Or is this just a niche material with limited use cases?
PLA’s Limitations and Why Strength Matters
PLA has long been the go-to filament for easy, hassle-free 3D printing. But when it comes to functional parts, its flaws become painfully obvious:
- Brittleness – Drop a PLA part, and there’s a good chance it snaps instead of flexing.
- Low Heat Resistance – Anything exposed to moderate heat (like a car dashboard) risks warping.
- Limited Impact Strength – PLA cracks under stress, making it unreliable for mechanical loads.
Contrast that with ABS, which can absorb impacts, or Nylon, which is flexible and tough. PLA prints beautifully but often fails when real strength is needed.
So why even bother with “high-strength PLA filament”? The answer depends on how strength is defined:
- Tensile Strength: Can it resist pulling forces?
- Impact Resistance: Will it break under sudden force?
- Structural Integrity: Does it hold up under continuous load?
For PLA filament to step up as a viable alternative, it needs to compete in at least one of these categories. That’s where reinforced blends come in, pushing PLA past its traditional weaknesses.
Advancements in High-Strength PLA: What’s Different?
So, how is PLA suddenly strong? The answer lies in reinforcement and formulation changes.
1. Reinforced Blends: Adding Toughness
Manufacturers have started infusing PLA with materials that enhance mechanical properties. These include:
- Carbon Fiber PLA – Improves rigidity and impact resistance.
- Glass-Filled PLA – Adds structural integrity without sacrificing ease of printing.
- High-Impact PLA – Proprietary blends focused on toughness and reduced brittleness.
These materials make PLA behave more like ABS or even Nylon in some cases, bridging the gap between convenience and durability.
2. Advanced Processing: Better Strength Without Additives
Beyond reinforcements, some high-strength PLA formulations rely on improved polymer structure alone.
- Annealable PLA – Can be heat-treated post-printing to increase durability.
- Modified molecular structure – Some blends optimize crystallization for stronger inter-layer adhesion.
3. Trade-offs and Considerations
While these advancements improve PLA’s strength, they come with a few caveats:
- Higher cost compared to regular PLA.
- Requires specialized printing settings (higher temps, controlled cooling).
- Not fully replacing ABS or Nylon but still viable for many functional parts.
High-strength PLA is becoming a legitimate option for mechanical applications, but is it strong enough for demanding prints? That depends on the use case, which leads us to…
Practical Applications: What Can You Print With It?
So, does high-strength PLA filament actually hold up in functional applications? The short answer: it depends on the type of stress the part will endure.
1. Where High-Strength PLA Filament Works Well
Certain applications benefit from PLA’s stiffness, dimensional stability, and ease of printing—especially with reinforced blends:
- Jigs & Fixtures: PLA’s rigidity makes it great for custom work-holding solutions.
- Brackets & Mounts: Stiff PLA blends can support moderate loads in non-flexing applications.
- Gears & Mechanical Parts: Carbon fiber PLA improves wear resistance, though load limits exist.
For projects where strength means rigidity, high-strength PLA can compete with ABS and even Nylon in some cases.
2. Where It Falls Short
Despite improvements, PLA still isn’t ideal for high-impact, high-flex applications:
- Car Parts & Outdoor Uses: Heat exposure still causes deformation over time.
- Load-Bearing Structures: Tough PLA works for moderate loads but lacks ductility.
- Shock-Absorbing Components: Nylon or TPU remain superior for absorbing impacts.
3. Putting It to the Test
Tests show carbon fiber-infused PLA is stronger than regular PLA, but still more brittle than ABS.
- Best for static loads rather than dynamic stress.
- Excellent for precision prints needing tight tolerances.
- Optimized with annealing to further enhance durability.
For functional prints that require both rigidity and reliability, high-strength PLA is no longer just hype—it’s a real contender. But does it replace ABS or Nylon entirely? Not quite.
Optimizing Prints for Maximum Strength
Even the best high-strength PLA filament can fail if printed incorrectly. To truly maximize strength, you need to optimize for:
1. Layer Adhesion: Strength Starts Here
Since 3D-printed parts are weakest along layer lines, improving adhesion is critical:
- Increase extrusion temperature (typically 10-20°C higher than standard PLA).
- Slow down print speed to allow better layer bonding.
- Use wider extrusion width for thicker, stronger walls.
2. Infill Matters: Density vs. Strength
A common mistake is assuming more infill = stronger parts. Instead, focus on:
- Grid or gyroid infill for impact resistance.
- Higher wall thickness (2-4 perimeters) rather than excessive infill.
- At least 40-50% infill for functional parts.
3. Print Orientation: Avoid Weak Layer Bonds
Printing orientation dramatically affects strength:
- Lay parts flat when possible—avoids vertical layer splitting.
- Align load-bearing stress along the strongest axis (test part orientation in CAD).
4. Post-Processing for Extra Durability
After printing, you can further increase strength with heat treatment:
- Annealing PLA (heating to ~80°C for 20-30 minutes) improves crystallization.
- Sanding + resin coating strengthens outer layers for wear resistance.
- Chemical strengthening (if applicable) can enhance durability.
5. Final Verdict: Is It Worth It?
With the right settings, high-strength PLA can rival ABS for certain applications. However, if your part needs impact resistance or flex, ABS or Nylon still hold the advantage.
Conclusion: Is High-Strength PLA Filament a Viable Alternative?
So, can high-strength PLA filament actually replace ABS, Nylon, or other rugged filaments? In some cases, yes—but not across the board.
For rigid functional parts, reinforced PLA blends offer significant strength improvements, making them viable for jigs, brackets, and precision components. With proper printing techniques and annealing, PLA can compete with ABS in certain load-bearing scenarios.
But PLA still has inherent weaknesses—it lacks heat resistance, struggles with high-impact applications, and isn’t as durable as Nylon for mechanical stress. If your project demands flexibility, heat tolerance, or serious impact resistance, PLA remains a secondary option.
Final Verdict:
- Use high-strength PLA if you need rigid, wear-resistant parts with minimal flex.
- Stick to ABS/Nylon if you need ductility, impact absorption, or heat resistance.
PLA has evolved far beyond its “beginner filament” reputation. While it won’t replace ABS entirely, it’s now a legitimate contender in functional 3D printing—as long as you know its strengths and limitations.
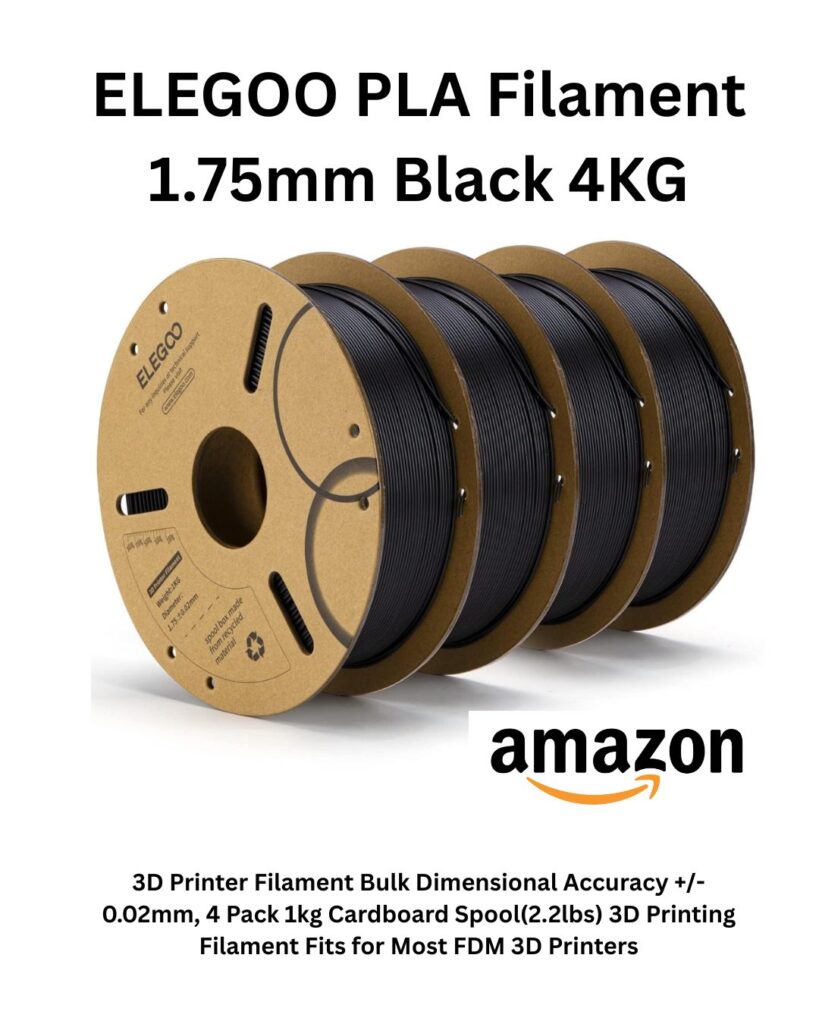
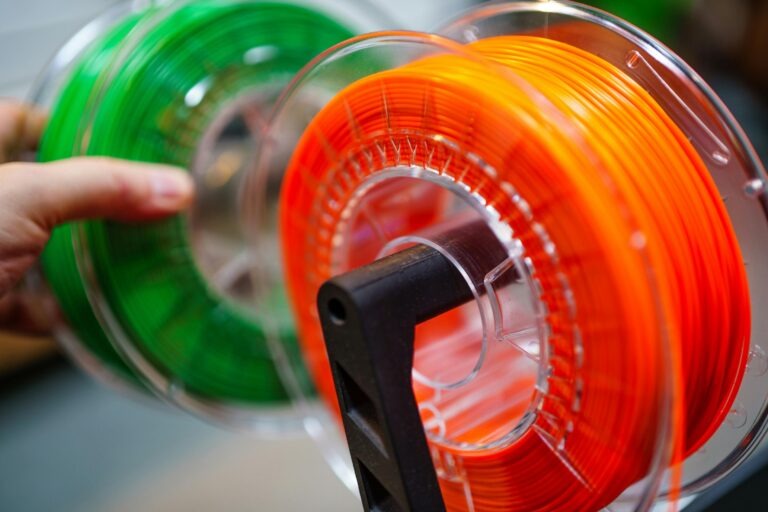
ABS Filament for Industrial Applications: Strength, Durability, and Versatility in Manufacturing
Using ABS filament for industrial applications is just right. Learn why. . .
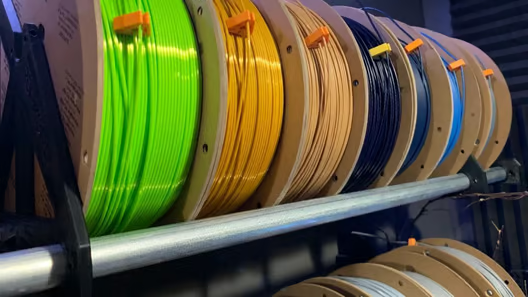
PETG Filament for Durable 3D Prints: A Comprehensive Guide
PETG combines strength, flexibility, and environmental durability, making it a top filament for functional parts.
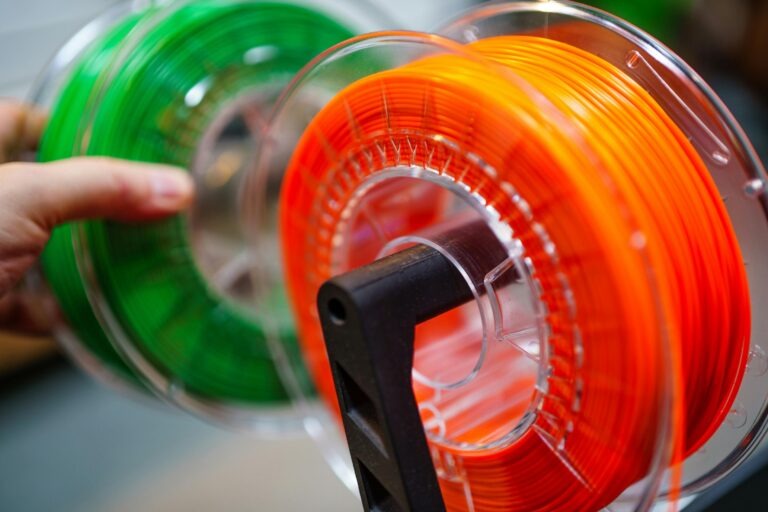
ABS Filament for Functional Parts: A Comprehensive Guide
ABS filament is one of the best choices for functional 3D-printed parts, offering durability, heat resistance, and impact strength.
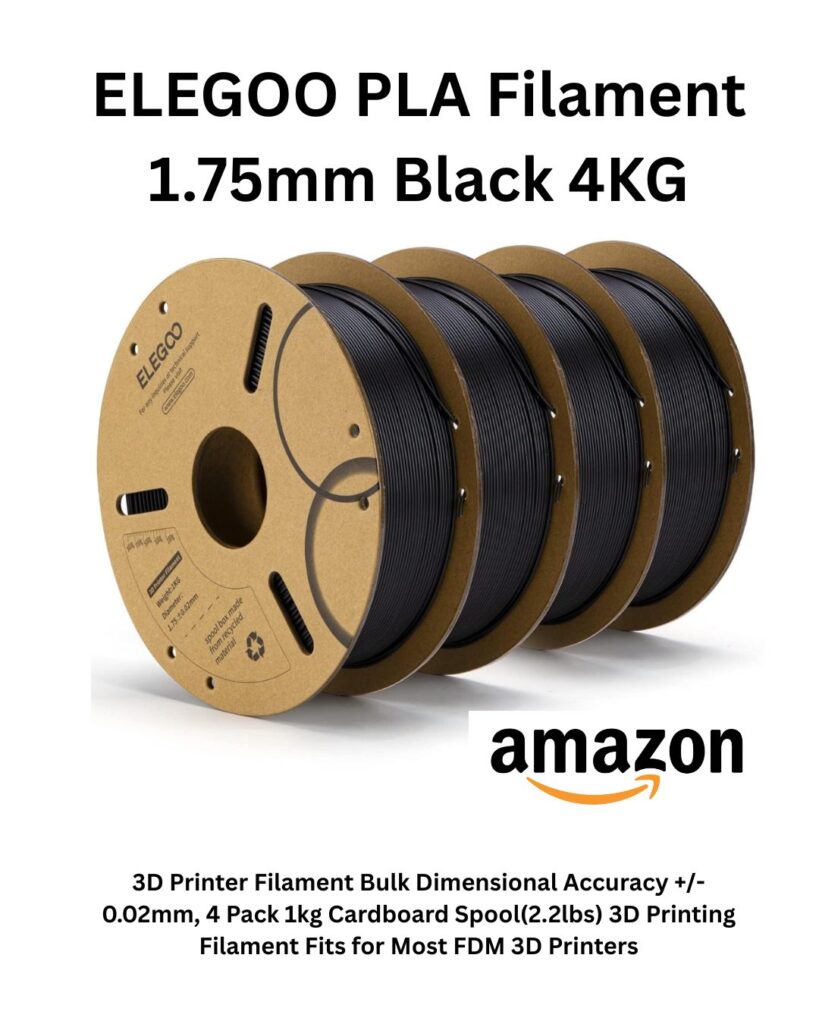
