
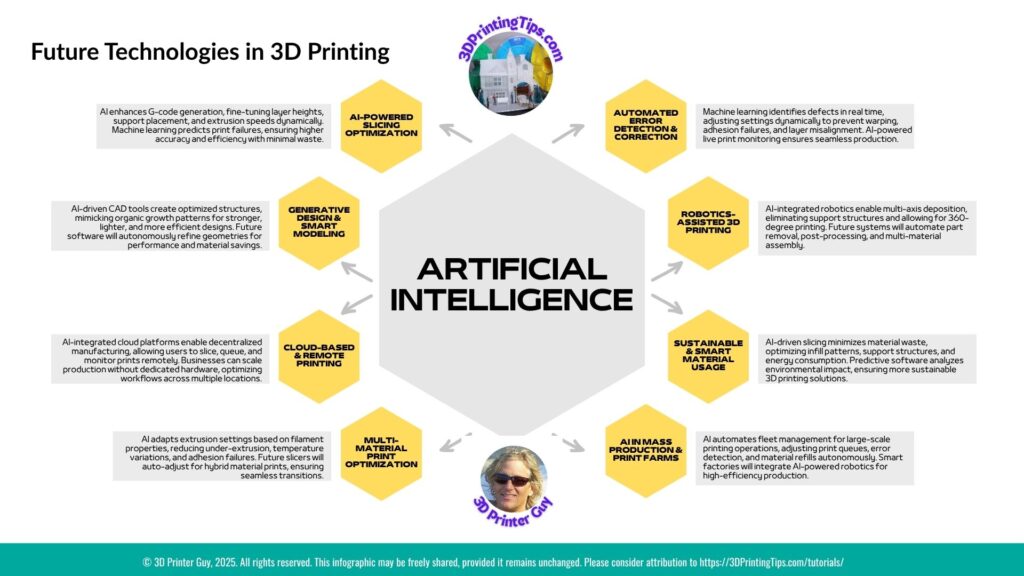
1. Introduction: The Future of 3D Printing Software
What do the Future technologies in 3D printing software hold for us? In the past decade, 3D printing software has undergone revolutionary advancements—moving beyond basic slicers to AI-driven, cloud-based, and automation-powered solutions. As the industry grows, so does the need for more intelligent, adaptable software that can optimize prints, reduce waste, and push the boundaries of design.
This evolution isn’t slowing down. The future of 3D printing software will likely be defined by AI-powered slicing algorithms, generative design tools, cloud computing, and robotics integration. As manufacturers and developers race to unlock new efficiencies, understanding where this technology is headed will ensure that makers, engineers, and businesses stay ahead of the curve.
In this article, we’ll explore:
✅ Emerging technologies shaping 3D printing software.
✅ AI-driven automation, generative design, and cloud-based slicing.
✅ Predictions for the next decade of 3D printing software advancements.
2. AI & Machine Learning as future technologies in 3D printing software
As 3D printing moves toward smarter automation, artificial intelligence (AI) and machine learning (ML) are revolutionizing the way we prepare, optimize, and execute prints. Gone are the days of manually tweaking slicer settings or adjusting print parameters through trial and error—today’s AI-driven software can predict failures, optimize supports, refine extrusion rates, and even repair flawed designs before printing begins.
📌 AI-Powered Slicing Optimization: Smarter G-code Generation
Traditional slicers rely on preset algorithms to determine layer height, extrusion speed, and support placement. AI-driven slicing engines, however, take a different approach—learning from past prints to continuously improve slicing decisions.
✅ How AI is improving slicing software:
- Adaptive Layer Height Adjustments: AI analyzes the model’s geometry and automatically adjusts resolution where needed, refining details while minimizing print time.
- Auto-Generated Optimized Supports: Machine learning algorithms predict structural weaknesses, dynamically creating the most efficient support structures.
- Real-Time Error Prevention: AI-powered slicing checks for potential adhesion problems, warping, or overhang failures, adjusting settings before printing starts.
🔹 Future Applications:
- AI could eventually self-adjust extrusion rates based on filament variability, ensuring uniform print quality.
- Machine learning-powered G-code refinements could reduce vibrations, improving print accuracy at high speeds.
📌 Real-Time Error Detection & Print Failure Prevention
Failed prints are a huge frustration for makers, but future 3D printing software aims to solve this problem before it even starts. AI-driven monitoring tools predict failures in real time, adjusting print settings dynamically to compensate for environmental changes like temperature shifts or filament inconsistencies.
✅ AI-powered failure prevention features:
- Live print monitoring with defect detection—AI can stop failed prints before they waste material.
- Smart bed leveling adjustments—Compensates for imperfections in print bed alignment.
- AI-enhanced slicing predictions—Identifies where a print might fail based on historical data.
🔹 Future Applications:
- AI-assisted real-time nozzle control, adjusting print speed when detecting inconsistencies.
- Thermal monitoring systems to prevent clogging or filament degradation.
📌 Adaptive Support Generation & Removal Optimization
One of the biggest challenges in 3D printing is support structure placement and removal. AI is making support generation more efficient, reducing material use while improving ease of removal.
✅ Key AI-driven support optimizations:
- Density-aware supports—AI adjusts density based on critical stress points, ensuring proper strength without excessive material use.
- Removable structure prediction—Analyzes potential damage risks and creates supports that detach smoothly post-print.
- Smart tree supports—AI generates precise branching patterns for strong yet minimal support placement.
🔹 Future Applications:
- Machine learning could create dynamic breakaway supports, reducing manual post-processing time.
- Automated adaptive support scaling for different filament types and extrusion settings.
📌 AI-Powered Mesh Repair & Print Optimization
Many 3D models contain imperfections, such as non-manifold edges, intersecting geometry, or holes that prevent successful slicing. AI-powered mesh repair tools fix these errors automatically, preparing models for flawless slicing and printing.
✅ How AI improves mesh repairs:
- Auto-healing algorithms fix broken geometry without manual intervention.
- Topology optimization for stronger mechanical parts and smoother organic designs.
- Auto-decimation tools reduce poly count for more efficient slicing.
🔹 Future Applications:
- AI-driven printability analysis, identifying weak points before printing starts.
- Automated lattice structuring for lightweight, strong prints.
📌 Conclusion: How AI is Shaping the Future of 3D Printing Software
AI-powered software is already transforming the way we prepare and optimize prints, reducing failures, improving support structures, and automating tedious slicing adjustments. As machine learning improves, future slicing tools will create near-perfect prints with minimal waste and maximum efficiency.
3. The Rise of Cloud-Based & Remote Printing as future technologies in 3D printing software
As 3D printing evolves, the demand for efficient, scalable, and decentralized production is driving the adoption of cloud-based slicing and remote printing technologies. Instead of being tied to a single workstation, users can now slice models, manage print jobs, and monitor progress from anywhere in the world.
Cloud-based slicing is particularly valuable for industrial applications, decentralized manufacturing, and remote collaboration, allowing teams to share optimized profiles, queue prints across multiple machines, and automate production workflows.
📌 Why Cloud-Based 3D Printing Software Is Gaining Popularity
Traditional 3D printing workflows require users to manually prepare and slice models on local machines, often leading to inefficiencies when dealing with large-scale projects or multi-printer setups. Cloud-based solutions address these problems by:
✅ Centralizing slicing operations – Instead of installing slicer software locally, users can access cloud-based tools via a web interface. ✅ Enabling remote job management – Print queue organization and monitoring happen in real time from any device. ✅ Standardizing slicing profiles – Teams can share optimized settings for filament types, printer models, and resolution preferences. ✅ Integrating AI-driven error detection – Cloud slicers can predict failures and optimize settings automatically before a print begins.
🔹 Future Application:
- Fully automated distributed 3D printing hubs, where cloud-connected printers function as part of a seamless production network.
📌 Cloud Slicers vs. Traditional Desktop Slicing Software
Feature | Cloud-Based Slicing | Traditional Desktop Software |
---|---|---|
Accessibility | Accessible from any device with an internet connection | Limited to a single local machine |
Processing Power | Can leverage server-grade computing for faster slicing | Restricted by user’s local hardware |
Collaboration | Teams can share optimized profiles and queue prints remotely | Requires manual file transfers between team members |
Automation | AI-driven optimizations, job scheduling, and failure prediction | Requires manual adjustments and monitoring |
Security & Offline Access | Dependent on internet availability | Fully local and private, but lacks cloud features |
📌 Key Players in Cloud-Based Slicing & Remote Printing
Several cutting-edge platforms are leading the charge in cloud slicing technologies:
🖥️ OctoPrint:
- Open-source printer management software for remote job control.
- Allows live webcam monitoring, temperature tracking, and print queue management.
- Supports plugins for automation, custom G-code control, and AI monitoring.
☁️ AstroPrint:
- Provides cloud-based slicing, print queue management, and AI-powered error detection.
- Allows users to slice and manage files remotely via a web interface.
- Integrates cloud storage for print files and historical job tracking.
🏭 UltiMaker Digital Factory:
- Designed for enterprise-level cloud manufacturing workflows.
- Offers fleet management tools for large-scale 3D printing operations.
- Implements predictive slicing and automated material tracking.
🔹 Future Application:
- The emergence of fully autonomous cloud-operated print farms, capable of managing hundreds of 3D printers remotely.
📌 The Future of Distributed 3D Printing Networks as future technologies in 3D printing software
The next phase of cloud-powered 3D printing will likely involve decentralized print farms, where businesses and individuals can tap into shared manufacturing resources instead of relying on personal hardware.
✅ How decentralized print networks will work:
- Users will upload designs to cloud platforms, where AI-driven slicers optimize settings and distribute jobs.
- Print hubs will automatically queue models for production, ensuring maximum efficiency across multiple printers.
- Organizations can offer cloud-based printing services, reducing hardware investment while expanding production capacity.
🔹 Potential Impact:
- Lower costs for individuals & businesses by eliminating the need for dedicated high-end printers.
- Accelerated mass customization, enabling scalable manufacturing with on-demand localized production.
📌 Conclusion: How Cloud-Based Printing Will Transform 3D Workflows
Remote slicing and cloud-powered automation are reshaping the future of 3D printing software. As AI-enhanced platforms, decentralized print farms, and scalable networked production take hold, users will experience faster, smarter, and more efficient workflows than ever before.
4. Generative Design & AI-Powered Modeling as future technologies in 3D printing software
As 3D printing continues to push boundaries, AI-powered generative design is revolutionizing how models are created. Instead of relying solely on human input, generative design leverages machine learning to create optimized, complex structures based on real-world constraints, such as material strength, load-bearing requirements, and environmental conditions.
This approach unlocks designs that traditional modeling software couldn’t conceive—organic, intricate structures that mimic natural growth patterns, resulting in superior performance and efficiency.
📌 How Generative Design Works in 3D Printing Software
Generative design isn’t just about automating the modeling process—it’s about creating designs that are stronger, lighter, and more efficient than human-designed models. AI algorithms analyze a set of design parameters, such as:
✅ Load-bearing requirements – AI optimizes geometry to minimize weight while maintaining strength. ✅ Material properties – Software tailors designs to specific filaments or resin types, improving print success. ✅ Environmental factors – AI adjusts structures for heat resistance, pressure durability, and aerodynamics. ✅ Manufacturing constraints – Ensures that designs can actually be printed efficiently based on available technology.
🔹 Future Applications:
- AI-assisted bio-inspired designs—software that mimics natural forms like bone structures or coral growth for optimal strength.
- Automated model refinement tools, where users input broad concepts and let AI generate precise CAD models.
📌 Real-World Impact: Generative Design in Industry
While generative modeling may sound futuristic, it’s already being widely adopted in industrial 3D printing. Major engineering firms, aerospace companies, and automotive manufacturers use AI-generated designs to reduce material costs and enhance durability.
✅ Airbus & Aerospace Components – Generative algorithms create lightweight aircraft components, reducing fuel costs. ✅ Automotive Engineering – AI designs stronger yet lighter chassis and interior parts, improving efficiency. ✅ Medical Prosthetics & Implants – Generative modeling adapts structures to patients’ unique physiological needs.
🔹 Future Applications:
- AI-driven real-time shape optimization—adjusting models dynamically as new data is fed into the system.
- Self-learning design systems, where the software learns from past print successes and failures to improve future outputs.
📌 AI-Generated Organic Structures & Nature-Inspired Forms
One of the most exciting aspects of AI-powered modeling is its ability to mimic biological growth patterns, resulting in intricate, efficient structures optimized for real-world use.
✅ Lattice & scaffold structures – Lightweight yet incredibly strong geometries, perfect for aerospace and medical applications. ✅ Parametric & algorithmic modeling – Dynamic design tools that adjust forms based on stress distribution and material properties. ✅ Multi-material fusion – AI-generated transition zones for smooth blending of rigid and flexible materials within a single print.
🔹 Future Applications:
- AI-driven automatic supports & infill—software that designs internal supports based on strength requirements, eliminating waste.
- Self-modifying designs—adaptive CAD tools that adjust in real time based on additional constraints fed into the program.
📌 Conclusion: How AI-Powered Modeling Will Change 3D Printing
Generative design and AI-driven modeling are reshaping how 3D models are conceived and manufactured. As software becomes more intelligent, models will evolve dynamically, resulting in lighter, stronger, and more efficient prints with minimal material waste.
5. Automation & Smart Materials in Future Slicers
Automation is rapidly transforming 3D printing software, making 3D slicing software smarter, more efficient, and capable of handling complex material profiles with minimal manual input. Future slicers will automatically adjust settings based on material properties, fine-tune extrusion patterns in real-time, and even anticipate and correct print failures before they occur.
By integrating machine learning, sensor feedback, and multi-material optimization, upcoming slicing software will take print preparation from a trial-and-error process to a streamlined automated system.
📌 How Automation is Improving Slicing & Print Efficiency
Traditional slicing software requires users to manually adjust layer height, infill density, print speed, and support structures—often leading to material waste and inefficient prints. Automated slicing solutions will eliminate these bottlenecks by using AI-powered workflows that:
✅ Automatically optimize settings based on material type, printer model, and environmental conditions. ✅ Fine-tune extrusion patterns dynamically to prevent over-extrusion and under-extrusion issues. ✅ Predict filament depletion and pause prints for seamless filament changes. ✅ Monitor print quality in real time using onboard sensors and AI analysis.
🔹 Future Applications:
- Fully self-calibrating slicers that require zero manual input.
- AI-driven adaptive layer heights, adjusting resolution dynamically.
📌 Smart Material Profiles: AI-Driven Filament Optimization
Slicing software is evolving to automatically recognize filament types, adjusting settings to compensate for differences in flexibility, strength, and adhesion properties.
✅ Filament Tracking & Adaptive Printing:
- AI detects filament type and adjusts extrusion, bed adhesion, and cooling settings accordingly.
- Prevents waste by dynamically optimizing print speed and temperature.
- Detects humidity-damaged filament and compensates in real time.
✅ Multi-Material Slicing Advancements:
- Allows hybrid material prints, blending flexible and rigid filaments seamlessly.
- AI predicts optimal transition zones to avoid material bleeding between sections.
- Self-adjusts filament retraction and flow rates for better adhesion.
🔹 Future Applications:
- Filament composition scanning, where embedded sensors analyze spool data in real time.
- AI formulating custom print profiles based on filament characteristics (color, additives, wear resistance).
📌 The Role of Sensors & Automated Error Prevention in Slicers
Future slicers will integrate sensor networks that monitor and adjust print settings automatically, eliminating common failures like warping, under-extrusion, and layer misalignment.
✅ Key AI-Sensor Integrations:
- Thermal sensors that adjust bed and nozzle temperatures dynamically.
- Vibration monitoring to prevent layer shifts and ghosting artifacts.
- Adaptive cooling algorithms that modify fan speeds based on layer height and filament composition.
🔹 Future Applications:
- Machine-learning-enhanced print recovery, stopping failed prints before material is wasted.
- Auto-detection of print defects, triggering adjustments mid-print without user intervention.
📌 Conclusion: How Automation Will Change 3D Printing Forever
As AI-powered automation and smart material integration continue evolving, the future of 3D printing slicing software will look drastically different from today. Instead of manually tweaking settings, printers will self-optimize print profiles, adjust materials dynamically, and predict failures before they happen—resulting in faster, more reliable prints with minimal waste.
🔜 Next up: Robotics & 3D Printing Software Convergence—where we explore how future slicers will integrate with multi-axis robotic systems for high-precision manufacturing.
6. Robotics & 3D Printing Software Convergence
As automation and AI continue to redefine 3D printing workflows, the next frontier is the integration of robotics into 3D printing software. Multi-axis robotic systems, real-time AI-driven print monitoring, and self-adjusting toolpaths are set to revolutionize high-precision manufacturing.
From automated robotic arms assisting with post-processing to fully AI-powered robotic print farms, the convergence of 3D printing software with robotics will drastically enhance efficiency, accuracy, and scalability.
📌 How Robotics is Changing 3D Printing Workflows
Traditional 3D printers operate on Cartesian X/Y/Z movements, limiting complex geometries that require support-free overhangs and multi-directional material deposition. Robotic systems remove these constraints by introducing:
✅ Multi-axis printing: Robots enable 360-degree deposition, eliminating support structures in certain designs. ✅ Real-time AI-assisted toolpath adjustments: Robotic printers adapt movements based on layer-by-layer analysis, ensuring higher precision. ✅ Post-print processing automation: Robotic arms clean, remove supports, and even assemble parts post-print.
🔹 Future Applications:
- Autonomous robotic print farms, capable of adjusting themselves for multi-day manufacturing operations.
- AI-enhanced material extrusion, where robotic systems monitor and correct filament flow dynamically.
📌 Multi-Axis Printing & Support-Free Designs
One of the most promising robotic integrations in 3D printing software is the ability to print without supports, thanks to multi-axis toolpaths. Instead of restricting movement to fixed horizontal layers, robotic printers tilt, rotate, and adjust extrusion angles dynamically, allowing for:
✅ Complex curved structures without supports. ✅ Organic shapes that are stronger and more lightweight. ✅ Reduced material waste due to smarter deposition paths.
🔹 Future Applications:
- AI-driven 6-axis robotic printers for precise aerospace and automotive components.
- Hybrid additive/subtractive systems, where robotic units print and refine parts within the same cycle.
📌 AI-Powered Robotic Print Farms
In large-scale production, print farms need constant monitoring, error detection, and efficiency improvements. Robotics combined with AI slicing software eliminate downtime and manual oversight, making print farms autonomous and self-sufficient.
✅ How robotic print farms work:
- Automated material refills & filament swaps—robots detect filament depletion and swap spools automatically.
- AI-driven post-print inspections—cameras and sensors identify defects and trigger reprints before production errors occur.
- Robotic arms for part handling—finished prints are removed, sorted, or assembled without human intervention.
🔹 Future Applications:
- Large-scale decentralized production hubs, where companies outsource printing to automated robotic factories.
- AI-optimized robotic finishing, reducing post-processing time with self-sanding, polishing, and post-curing capabilities.
📌 Conclusion: Robotics Will Define the Future of Large-Scale 3D Printing
With multi-axis robotic integration, AI-powered error detection, and automation-driven print farms, 3D printing software will increasingly merge with robotics for precision, scalability, and efficiency. The next generation of printers may no longer resemble traditional machines—but rather autonomous robotic units built to optimize every stage of production.
🔜 Next up: Industry Predictions: The Future of 3D Printing Software—where we explore expert insights, market trends, and innovations expected in the next decade.
7. Industry Predictions: The Future of 3D Printing Software
The next decade will see 3D printing software evolve beyond manual slicers and CAD tools, shifting toward AI-driven automation, cloud-based workflows, and robotic integration. As new technologies emerge, we’ll likely witness faster, smarter, and more accessible printing solutions that redefine manufacturing, prototyping, and creative design.
📌 Major Trends Defining the Next Decade
✅ AI-Enhanced Slicing & Auto-Optimization
- AI will eliminate manual slicing adjustments, fine-tuning settings based on print history.
- Self-learning algorithms will anticipate print errors before they happen.
- Dynamic real-time adjustments will optimize supports, layer heights, and infill density.
✅ Cloud-Based & Remote Manufacturing
- AI-connected print farms will allow decentralized production hubs.
- Instant remote slicing & print queue management from any device.
- Collaboration tools will enable shared printing profiles and optimized settings across teams.
✅ Generative AI-Driven Modeling
- AI-powered CAD assistants will refine geometry for strength, weight, and material efficiency.
- Organic generative structures will improve aerospace, medical, and automotive applications.
- Parametric and AI-assisted automated design iterations will reduce product development cycles.
✅ Robotic 3D Printing Integration
- Multi-axis robotic printing will enable complex geometries without supports.
- Autonomous AI-controlled print farms will revolutionize scalable manufacturing.
- Hybrid additive/subtractive robotic systems will allow printing + post-processing in a single workflow.
📌 Industry Experts Weigh In
Leading experts predict that AI-enhanced automation, cloud slicing, and robotic precision will make 3D printing faster, cheaper, and more accessible. As software becomes smarter and more integrated into manufacturing workflows, businesses will increasingly shift toward AI-powered, error-free production methods.
🔹 Future Applications:
- AI-driven predictive design modifications, refining prints before slicing even begins.
- Blockchain-powered verification for material tracking & authenticity assurance.
- Self-calibrating, zero-maintenance printers using AI-guided diagnostics.
📌 Conclusion: The Next Era of 3D Printing Software
The next 10 years of 3D printing software will focus on automation, efficiency, and intelligent design tools, enabling AI-driven model creation, seamless cloud slicing, and robotics-powered precision printing. As these innovations unfold, 3D printing will become more accessible, scalable, and integrated into mainstream manufacturing.
8. Overall Conclusion: A Resource Built for Long-Term Relevance
With advancements in AI-driven slicing, cloud-based automation, and multi-axis robotic printing, this page serves as a permanent industry reference, ensuring readers stay ahead of the curve in 3D printing software evolution.
🚀 Bookmark this page and check back for updates as the industry evolves!
